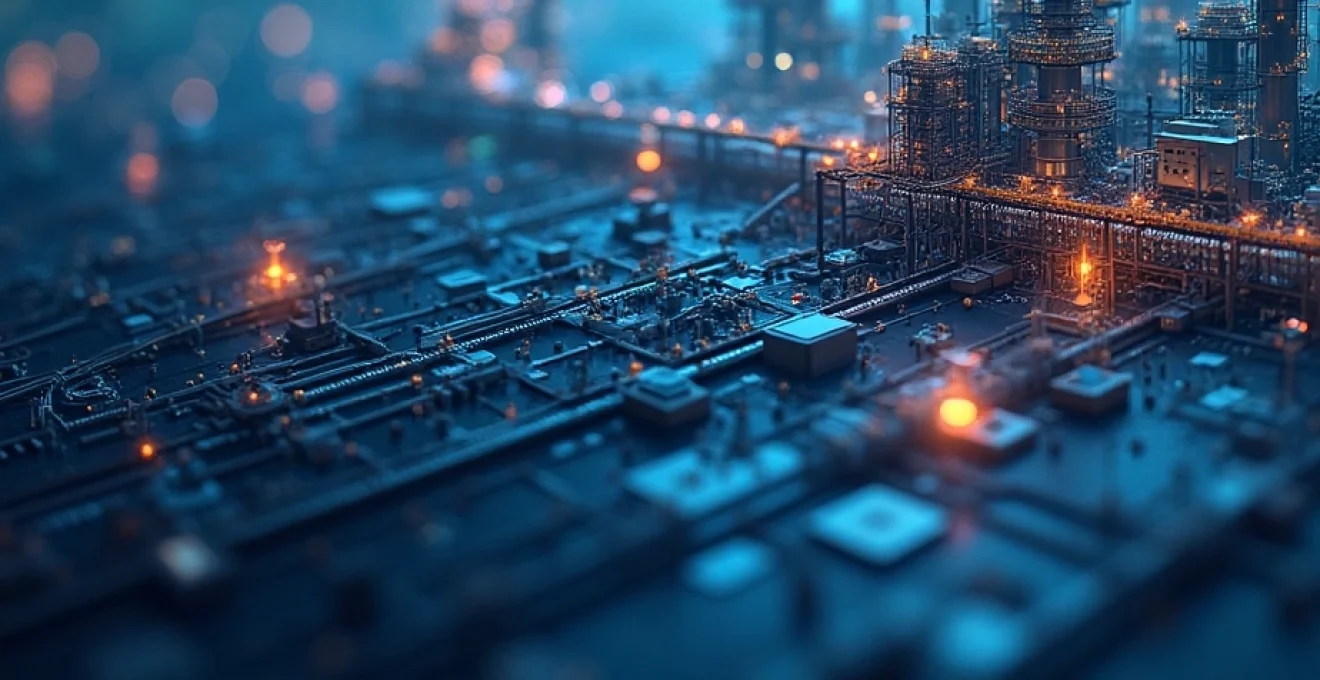
Dans le monde industriel moderne, la surveillance continue des installations est devenue un élément crucial pour garantir la productivité, la sécurité et la fiabilité des opérations. Les avancées technologiques ont considérablement amélioré notre capacité à collecter, analyser et exploiter les données en temps réel, ouvrant ainsi de nouvelles perspectives pour optimiser les processus et prévenir les incidents. Comment les entreprises peuvent-elles tirer parti de ces innovations pour mettre en place un système de monitoring efficace ? Quels sont les outils et méthodes les plus performants pour assurer un suivi permanent des installations industrielles ?
Systèmes de surveillance continue pour installations industrielles
Les systèmes de surveillance continue constituent la pierre angulaire d’un monitoring efficace des installations industrielles. Ces solutions intégrées permettent de collecter, traiter et analyser en temps réel une multitude de données provenant de divers capteurs et équipements répartis sur l’ensemble du site. L’objectif principal est de fournir une vision globale et détaillée de l’état de fonctionnement des installations, permettant ainsi une prise de décision rapide et éclairée en cas d’anomalie ou de dysfonctionnement.
Un système de surveillance continue typique comprend plusieurs composants clés. Tout d’abord, un réseau de capteurs intelligents est déployé stratégiquement sur l’ensemble de l’installation pour mesurer divers paramètres tels que la température, la pression, les vibrations ou encore les niveaux de fluides. Ces capteurs sont connectés à un système central de collecte et de traitement des données, généralement basé sur une architecture SCADA (Supervisory Control and Data Acquisition) ou un système de contrôle-commande industriel moderne.
L’intégration de technologies d’analyse avancées, telles que l’intelligence artificielle et le machine learning, permet d’exploiter pleinement le potentiel des données collectées. Ces outils sont capables de détecter des tendances subtiles, de prédire les défaillances potentielles et d’optimiser les processus de maintenance, contribuant ainsi à améliorer significativement la disponibilité et la performance des équipements.
Technologies de capteurs avancées pour le monitoring en temps réel
La qualité et la précision des données collectées sont essentielles pour un monitoring efficace. Les technologies de capteurs ont connu des avancées considérables ces dernières années, offrant des solutions de plus en plus performantes et adaptées aux environnements industriels exigeants. Voici un aperçu des principales technologies de capteurs utilisées pour le monitoring en temps réel :
Capteurs IoT et réseaux sans fil pour la collecte de données
L’Internet des Objets (IoT) a révolutionné la collecte de données dans le secteur industriel. Les capteurs IoT, combinés à des réseaux sans fil robustes, permettent de déployer rapidement et à moindre coût une infrastructure de surveillance étendue. Ces capteurs sont capables de mesurer une grande variété de paramètres et de transmettre les données en temps réel à un système central, offrant ainsi une flexibilité et une scalabilité inégalées.
Les réseaux sans fil industriels, tels que le Wi-Fi industriel, le Bluetooth Low Energy (BLE) ou les technologies LPWAN comme LoRaWAN, offrent des solutions adaptées à différents besoins en termes de portée, de consommation énergétique et de débit de données. La sélection de la technologie appropriée dépend des spécificités de l’installation et des exigences de monitoring.
Analyse vibratoire et acoustique avec accéléromètres
L’analyse vibratoire est une technique puissante pour évaluer l’état de santé des équipements rotatifs tels que les moteurs, les pompes ou les compresseurs. Les accéléromètres modernes, couplés à des algorithmes d’analyse avancés, permettent de détecter précocement des anomalies telles que les désalignements, les déséquilibres ou l’usure des roulements. Cette approche proactive de la maintenance contribue à réduire les temps d’arrêt imprévus et à optimiser les coûts de maintenance.
En complément de l’analyse vibratoire, l’analyse acoustique offre des informations précieuses sur l’état de fonctionnement des équipements. Les capteurs acoustiques peuvent détecter des fuites, des cavitations ou des frictions anormales, fournissant ainsi des indications précoces sur des problèmes potentiels.
Imagerie thermique et caméras infrarouges pour la détection d’anomalies
L’imagerie thermique est devenue un outil incontournable pour la détection d’anomalies dans les installations industrielles. Les caméras infrarouges permettent de visualiser la distribution de température sur les équipements et les structures, révélant ainsi des problèmes tels que des surchauffes localisées, des isolations défectueuses ou des fuites de fluides. Cette technologie non invasive offre une méthode rapide et efficace pour identifier des problèmes potentiels avant qu’ils ne deviennent critiques.
Les caméras thermiques modernes, équipées de capteurs haute résolution et d’algorithmes d’analyse d’image avancés, peuvent être intégrées dans des systèmes de surveillance automatisés. Elles permettent ainsi un monitoring continu des zones critiques, avec des alertes en temps réel en cas de détection d’anomalies thermiques.
Capteurs de pression et de débit pour le suivi des fluides
Dans de nombreuses installations industrielles, le suivi précis des pressions et des débits de fluides est crucial pour garantir l’efficacité des processus et prévenir les incidents. Les capteurs de pression et de débit modernes offrent une précision et une fiabilité accrues, même dans des conditions difficiles telles que des températures extrêmes ou des environnements corrosifs.
L’intégration de ces capteurs dans un système de monitoring global permet de surveiller en temps réel les performances des systèmes hydrauliques, pneumatiques ou de traitement des fluides. Des algorithmes d’analyse avancés peuvent détecter des tendances anormales, prédire des défaillances potentielles ou identifier des opportunités d’optimisation des processus.
Plateformes logicielles de gestion centralisée des données
La collecte de données à partir de multiples sources ne suffit pas à elle seule à assurer un monitoring efficace. Il est essentiel de disposer de plateformes logicielles puissantes pour centraliser, traiter et analyser ces données de manière cohérente. Ces plateformes jouent un rôle crucial dans la transformation des données brutes en informations exploitables pour la prise de décision.
SCADA et systèmes de contrôle-commande industriels
Les systèmes SCADA (Supervisory Control and Data Acquisition) et les systèmes de contrôle-commande industriels modernes constituent le cœur des plateformes de gestion centralisée des données. Ces solutions offrent une interface unifiée pour la supervision et le contrôle des processus industriels, intégrant les données provenant de multiples sources en temps réel.
Les systèmes SCADA modernes vont au-delà de la simple visualisation des données. Ils intègrent des fonctionnalités avancées telles que l’analyse prédictive, la gestion des alarmes intelligentes et l’optimisation des processus basée sur l’IA. Ces capacités permettent non seulement de réagir rapidement aux incidents, mais aussi d’anticiper les problèmes potentiels et d’optimiser proactivement les performances des installations.
Tableaux de bord et visualisation des KPI en temps réel
La visualisation efficace des données est essentielle pour permettre une compréhension rapide et intuitive de l’état des installations. Les plateformes modernes de gestion des données offrent des outils puissants pour créer des tableaux de bord personnalisés, présentant les indicateurs clés de performance (KPI) les plus pertinents pour chaque niveau de l’organisation.
Ces tableaux de bord en temps réel permettent aux opérateurs et aux gestionnaires de surveiller l’état global des installations d’un seul coup d’œil, tout en offrant la possibilité d’approfondir l’analyse sur des points spécifiques. L’utilisation de techniques de visualisation avancées, telles que les graphiques interactifs ou les représentations 3D des installations, améliore la compréhension et facilite la prise de décision rapide.
Intégration des données multi-sources avec l’OPC UA
L’intégration harmonieuse des données provenant de sources hétérogènes est un défi majeur dans les environnements industriels complexes. Le protocole OPC UA (Open Platform Communications Unified Architecture) s’est imposé comme un standard pour l’interopérabilité des systèmes industriels, facilitant l’échange de données entre différents équipements et systèmes.
L’OPC UA offre une approche standardisée pour l’intégration des données, permettant de créer une représentation unifiée de l’ensemble des installations. Cette intégration facilite non seulement la collecte et l’analyse des données, mais aussi la mise en place de systèmes de contrôle et d’optimisation plus sophistiqués, exploitant pleinement les synergies entre différents processus et équipements.
Stockage et analyse big data pour l’historisation long-terme
La gestion efficace des données historiques est cruciale pour l’analyse des tendances à long terme et l’optimisation continue des processus. Les plateformes de gestion des données industrielles intègrent désormais des capacités de stockage et d’analyse Big Data, permettant de conserver et d’exploiter des volumes massifs de données sur de longues périodes.
Ces solutions de stockage à long terme, souvent basées sur des technologies de bases de données distribuées, offrent non seulement une grande capacité mais aussi des performances élevées pour l’analyse de données historiques. Couplées à des outils d’analyse avancés, elles permettent de découvrir des tendances subtiles, d’effectuer des analyses comparatives approfondies et d’alimenter des modèles prédictifs de plus en plus sophistiqués.
Intelligence artificielle et apprentissage automatique pour la maintenance prédictive
L’intégration de l’intelligence artificielle (IA) et de l’apprentissage automatique dans les systèmes de monitoring industriel a ouvert de nouvelles perspectives pour la maintenance prédictive. Ces technologies permettent d’analyser des volumes massifs de données pour détecter des schémas complexes et prédire les défaillances avant qu’elles ne se produisent, offrant ainsi un potentiel considérable pour réduire les temps d’arrêt et optimiser les coûts de maintenance.
Modèles de détection d’anomalies par machine learning
Les modèles de détection d’anomalies basés sur le machine learning représentent une avancée significative par rapport aux méthodes traditionnelles basées sur des seuils prédéfinis. Ces modèles sont capables d’apprendre les comportements normaux des équipements à partir des données historiques et de détecter des déviations subtiles qui pourraient indiquer un problème naissant.
L’utilisation d’algorithmes tels que les forêts d’isolation ou les réseaux de neurones auto-encodeurs permet de détecter des anomalies multidimensionnelles, prenant en compte simultanément plusieurs paramètres pour identifier des comportements anormaux. Cette approche holistique améliore considérablement la précision de la détection et réduit les faux positifs, permettant ainsi une maintenance plus ciblée et efficace.
Prévision des pannes avec les réseaux de neurones LSTM
Les réseaux de neurones récurrents, en particulier les architectures LSTM (Long Short-Term Memory), se sont révélés particulièrement efficaces pour la prévision des pannes dans les environnements industriels. Ces modèles sont capables de capturer des dépendances temporelles complexes dans les séries de données, permettant ainsi de prédire avec précision l’évolution de l’état des équipements.
En analysant les tendances historiques et les conditions actuelles, les modèles LSTM peuvent estimer la probabilité de défaillance d’un équipement dans un futur proche, permettant ainsi une planification proactive de la maintenance. Cette approche prédictive permet non seulement de réduire les temps d’arrêt imprévus mais aussi d’optimiser les interventions de maintenance, en les programmant au moment le plus opportun.
Optimisation des interventions par algorithmes génétiques
Une fois les défaillances potentielles identifiées, l’optimisation des interventions de maintenance devient cruciale pour maximiser l’efficacité opérationnelle. Les algorithmes génétiques, inspirés des principes de l’évolution naturelle, offrent une approche puissante pour résoudre ce problème d’optimisation complexe.
Ces algorithmes peuvent prendre en compte de multiples facteurs tels que la criticité des équipements, les coûts d’intervention, les contraintes de ressources et les dépendances entre les différents composants pour générer des plannings de maintenance optimisés. En itérant sur de nombreuses générations de solutions, les algorithmes génétiques peuvent identifier des stratégies d’intervention qui minimisent les temps d’arrêt tout en respectant les contraintes opérationnelles et budgétaires.
Cybersécurité et protection des systèmes de monitoring industriel
Avec la numérisation croissante des systèmes industriels, la cybersécurité est devenue un enjeu majeur pour les systèmes de monitoring. Les installations industrielles, autrefois isolées, sont désormais de plus en plus connectées, augmentant ainsi leur exposition aux cybermenaces. La protection de ces systèmes critiques nécessite une approche multidimensionnelle, combinant des mesures techniques, organisationnelles et humaines.
La mise en place d’une architecture de sécurité robuste est essentielle. Cela inclut la segmentation des réseaux, l’utilisation de pare-feux industriels spécialisés, et la mise en œuvre de protocoles de communication sécurisés. L’authentification forte et la gestion rigoureuse des accès sont également cruciales pour prévenir les accès non autorisés aux systèmes de contrôle et de monitoring.
La formation et la sensibilisation du personnel jouent un rôle clé dans la stratégie de cybersécurité. Les employés doivent être formés pour reconnaître les menaces potentielles et suivre les meilleures pratiques en matière de sécurité. Des audits réguliers et des tests de pénétration permettent d’identifier et de corriger les vulnérabilités avant qu’elles ne soient exploitées par des acteurs malveillants.
Méthodologies d’implémentation et bonnes pratiques opérationnelles
La mise en place d’un système de monitoring efficace nécessite une approche méthodique et structurée. Voici
Audit initial et cartographie des points de mesure critiques
La première étape cruciale dans l’implémentation d’un système de monitoring efficace est la réalisation d’un audit initial approfondi. Cet audit vise à identifier les points de mesure critiques au sein de l’installation, en tenant compte des processus clés, des équipements essentiels et des zones à risque. Une cartographie détaillée de ces points de mesure permet d’optimiser le déploiement des capteurs et d’assurer une couverture complète des éléments cruciaux pour la performance et la sécurité de l’installation.
Lors de cet audit, il est important d’impliquer les différentes parties prenantes, notamment les opérateurs, les ingénieurs de maintenance et les responsables de production. Leur expertise combinée permet d’identifier non seulement les points de mesure évidents, mais aussi les zones potentiellement problématiques qui pourraient échapper à une analyse superficielle. Cette approche collaborative garantit que le système de monitoring répond aux besoins réels de l’installation et s’aligne sur les objectifs opérationnels de l’entreprise.
Définition des seuils d’alerte et plans d’action associés
Une fois les points de mesure critiques identifiés, l’étape suivante consiste à définir des seuils d’alerte précis pour chaque paramètre surveillé. Ces seuils doivent être établis en tenant compte des spécifications des équipements, des normes de l’industrie et de l’expérience opérationnelle. Il est crucial de trouver le juste équilibre entre la sensibilité nécessaire pour détecter les anomalies précoces et la robustesse pour éviter les faux positifs qui pourraient saturer le système d’alertes.
Pour chaque seuil d’alerte, un plan d’action clair et détaillé doit être élaboré. Ces plans d’action définissent les étapes à suivre en cas de dépassement des seuils, spécifiant les responsabilités, les procédures d’escalade et les mesures correctives à mettre en œuvre. L’automatisation de certaines réponses peut être envisagée pour les situations critiques nécessitant une réaction immédiate, tandis que d’autres alertes peuvent déclencher une analyse plus approfondie avant toute intervention.
Formation des opérateurs et gestion du changement
L’introduction d’un nouveau système de monitoring représente un changement significatif dans les pratiques opérationnelles. Une formation approfondie des opérateurs et du personnel de maintenance est essentielle pour garantir une utilisation efficace du système. Cette formation doit couvrir non seulement les aspects techniques de l’utilisation des outils de monitoring, mais aussi l’interprétation des données et la prise de décision basée sur les informations fournies par le système.
La gestion du changement est un aspect crucial de l’implémentation. Il est important de communiquer clairement les bénéfices du nouveau système, d’impliquer les utilisateurs finaux dans le processus de déploiement et de recueillir régulièrement leurs retours pour améliorer continuellement le système. Des sessions de formation régulières et des mises à jour sur les nouvelles fonctionnalités ou les améliorations du système contribuent à maintenir l’engagement des équipes et à maximiser l’utilisation efficace des outils de monitoring.
Processus d’amélioration continue du système de monitoring
Un système de monitoring efficace n’est pas statique ; il doit évoluer constamment pour s’adapter aux changements dans les processus de production, aux nouvelles technologies et aux besoins changeants de l’entreprise. La mise en place d’un processus d’amélioration continue est essentielle pour maintenir la pertinence et l’efficacité du système de monitoring à long terme.
Ce processus d’amélioration continue implique plusieurs aspects. Tout d’abord, une revue régulière des indicateurs de performance du système de monitoring lui-même, tels que la précision des alertes, les temps de réponse et l’impact sur la réduction des temps d’arrêt. Ensuite, l’analyse des tendances à long terme des données collectées peut révéler des opportunités d’optimisation des processus ou de prévention des problèmes récurrents. Enfin, la veille technologique et l’évaluation continue des nouvelles solutions de monitoring permettent d’identifier des opportunités d’amélioration et d’intégration de technologies innovantes pour renforcer les capacités du système.
En conclusion, le monitoring permanent des installations industrielles est devenu un élément incontournable pour assurer la performance, la fiabilité et la sécurité des opérations. Les technologies avancées de capteurs, combinées à des plateformes logicielles puissantes et à l’intelligence artificielle, offrent des possibilités sans précédent pour optimiser les processus et prévenir les incidents. Cependant, le succès d’un système de monitoring repose non seulement sur la technologie, mais aussi sur une approche méthodique d’implémentation, une formation adéquate du personnel et un engagement continu dans l’amélioration du système. En adoptant ces outils et méthodes, les entreprises peuvent transformer leur approche de la gestion des installations, passant d’une posture réactive à une stratégie proactive et prédictive, garantissant ainsi une compétitivité accrue dans un environnement industriel en constante évolution.